Ag Partners Unit Train Loading Facility
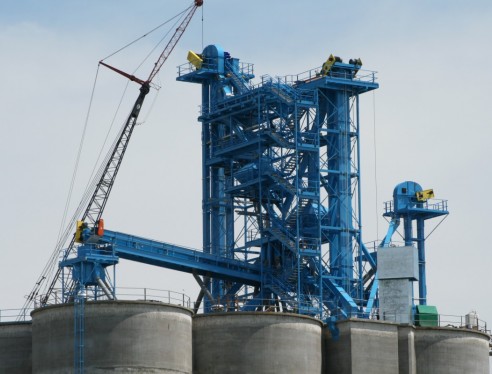
After the devastation of a grain dust explosion, Younglove was selected to construct a replacement rail loadout facility consisting of six 40-foot-diameter silos with eight interstice bins. Receiving of trucked grain is through one 20,000- and two 15,000-bushel-per-hour bucket elevators. Received grain is then scalped over two 15,000-bushel-per-hour drag scalpers and cleaned over two 16,000-bushel-per-hour gravity cleaners. Grain is then distributed through dual rotary distributors to the silos either by gravity or a 15,000-bushel-per-hour transfer conveyor.
Reclaim of wet corn from the silos or interstice bins is through a 10,000-bushel-per-hour drag conveyor to a 7,000-bushel-per-hour grain dryer. The reclaim of grain to the rail loadout bin is through a 30,000-bushel-per-hour drag conveyor and the combined use of two 15,000-bushel-per-hour receiving legs. The rail loadout system is rated at 60,000 bushels per hour. Grain is reclaimed to rail loadout through a 60,000-bushel-per-hour bulk scale and then through a 60,000-bushel-per-hour grain sampler to rail loadout. Six silos have 1/10 cfm aeration.
Temperature detection cables are located in each of the six silos and one interstice bin, allowing for continuous readout.
At the three receiving bucket elevators, a mineral oil dust suppression system was installed in the boot pocket inlets. The truck receiving pits have aspiration pickup for continuous dust control.
The grain complex is fully automated from receiving to distribution to reclaim to rail loadout.